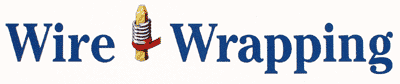
In 1952, a new technology was discovered by The Bell Laboratory, Western
Electric Company to form a consistent gas-tight electrical connection by
tightly wrapping wire around a terminal with two sharp edges. This advanced
technology would open the door to meet the needs of more complex electronic
equipment, allowing for more terminals in less space. Since then, the electronic,
telecommunication and aviation industries have recognized wire wrapping
as the most reliable, stable and common method of connecting signal and
power terminals in todays advanced work force.
Wire Wrap Guide:
How
to Make Wire Wrapped Connections
Helpful Wire Wrapping
Tips
Common Wire Wrapping
Problems
Wire Wrap Glossary
How
to Make Wire Wrapped Connections
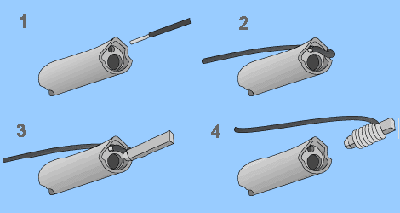
Step 1: Insert the pre-stripped wire into the wire slot of the wrapping
bit.
Step 2: Anchor the wire in the notch of the wrapping sleeve.
Step 3: Insert the terminal into the center hole of the wrapping bit.
Step 4: Activate the wire wrapping tool. This rotates the wrapping bit and
wraps the wire around the terminal.
Helpful
Wire Wrapping Tips
Coiling the wires around the sharp corners of a .025 in. square
receptacle post creates a wire wrapped termination.
A clean metal-to-metal contact between the wire and the post
can be achieved by bending the wire around the sharp corner, breaking the
oxide layer of both surfaces, thus revealing an oxide-free surface.
Try to avoid kinks in the wire when stripping.
Dont use wire that will break easily.
The minimum number of turns is based on wire gauge and the
type of wrap.
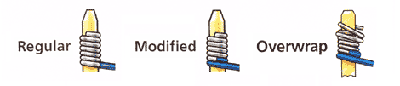
Standard Wrap = Coils bare wire only around the post
Modified Wrap = Coils the wire and a portion of insulation
increasing the ability to withstand vibration.
When using wire wrap guns, make sure to not hold too tightly
against the board to prevent bunched up, messy coils around the base of
the post.
Holding a wrap gun with too little pressure can result in
spaces between the coils on the post, making the post visible.
Pulling the trigger of the wrap gun too hard will result in
broken wire inside the gun barrel.
Backforce features on electric wrap guns are important
to prevent against overwrapping from excessive force.
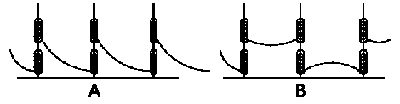
Proper Daisy Chain wiring several points together can
be easy if done correctly. Figure A and B show the proper and improper way
to daisy chain. If a mistake was made, the entire wire would have to be
unwrapped in Figure A. In contrast, Figure B you would have at the most
three wires to unwrap to remove any wire in the chain. This is the preferred
approach.
Common
Wire Wrapping Problems:
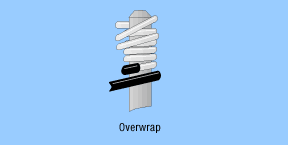
The Overwrap - Dont press too hard! Wires will slip
over the preceding turn if you push down too hard on the wrap tool while
turning. Make sure to practice to ensure a quality connection.
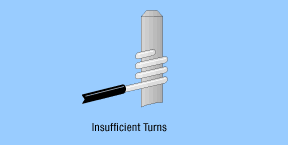
Insufficent Turns Push wire all the way into wire slot. Improperly
feeding of wire into the wire slot of the bit results in insufficient turns
of wire for regular wraps or insufficient insulation turns for modified
wraps.
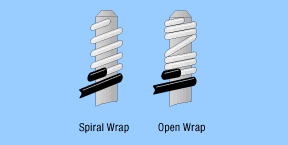
Spiral Wrap/ Open Wrap Dont remove the tool too quickly! Wire
turns more than 0.005 inches apart, called spiral or open wraps, are caused
by too rapid a removal of the wrapping tool.
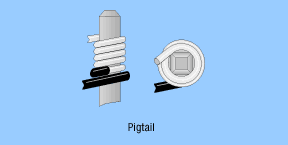
Pigtails Select the proper bit and sleeve. When a wire has not been
completely wrapped the result is a pigtail. This results if
the size of the bit is improperly matched to the terminal diagonal.
Wire
Wrap Glossary
Anti-Backforce
(ABF): This means that the gun, whether electric or pneumatic, has a
spring mechanism behind the wire wrapping bit. When the operator pulls the
trigger the spring will compress causing the bit to recede back into the
wire wrapping sleeve. This allows the operator who is inexperienced to wrap
perfectly everytime.
AWG: Abbreviation for American Wire Gauge
Bare Wire: Bare wire refers to the wire after the insulation has
been removed or wire which is produced without insulation.
Bit Radius: This is the distance from the center of the terminal
hole of the wire wrap bit to the outside wall of the wire wrap sleeve. This
information is used to determine if there is enough space between pins for
a wire wrapping bit and sleeve to fit.
Carpel Tunnel Syndrome: This medical symptom is sometimes attributed
to repetitive motion injuries usually caused by a tool that is not ergonomically
designed for the operator.
cfm: Abbreviation for cubic feet per minute.
Funnel:
This term refers to the end of the wire wrapping sleeve where the wire
is inserted. The point where the wire is inserted the end of the wire
wrap sleeve has been flared to make it easier to insert the wire.
in: Abbreviation for inch(es).
Insulated Sleeve: This term refers to a wire wrapping sleeve
where shrink wrap has been shrunk around the wire wrap sleeve. This
plastic wrap insulates the sleeve from any electrical current which
might be passing through the wire wrapping pin at the time.
kg: Abbreviation for kilogram(s).
Kynar wire: This refers to the type of insulation which is surrounding
the wire. Other types of insulation which we do not recommend are tefzel
and teflon.
Modified Wrap: The first 1/2 to 2 wraps are made with insulation
wrapped around the terminal post. These wraps are in addition to the
recommended wraps made with bare wire.
mm: Abbreviation for millimeter(s).
No Funnel: This term refers to a wire wrapping sleeve in which
the end of the sleeve has not been flared, basically a straight tube.
Notch: This term refers to two small half circles which appear
on the sides of the wire wrap sleeve where the wire enters. Once the
wire has been placed into the bit and sleeve the remainder is placed
into the notch so that it will not be pinched when pushed down around
the terminal post.
Notch Depth: This term refers to the depth of the notch which
appears on both sides of the end of a wire wrapping sleeve.
Notch Width: This terms refers to the width of the notch which
appears on both sides of the end of a wire wrapping sleeve.
NPT: Abbreviation for National Pipe Thread
oz: Abbreviation for ounce(s).
PSIG: Abbreviation for pounds per square inch gauge.
RPM: Abbreviation for revolutions per minute.
Sleeve Thickness: This terms refers to the actual thickness of
the wall of the wire wrapping sleeve.
Slim Nose: This term refers to a wire wrapping sleeve in which
the end of the sleeve where the wire is inserted is tapered down to
a smaller outside diameter. This type of sleeve allows the operator
to wire wrap in areas where the spacing between pins is unusually tight.
Standard: This term refers to a standard wire wrapping gun which
does not have ABF.
Standard Wrap: This term refers to the fact that only bare wire
is wrapped to the terminal post.
Terminal Diagonal: This term refers to the distance between two
opposite points which are the furtherest apart on a wire wrapping terminal
post.
Terminal Hole Depth: This term refers to depth of the hole in
the wire wrapping bit which is seen at the end of the bit.
Terminal Hole Diameter: This term refers to the diameter of the
hole in a wire wrapping bit which is seen at the end of the bit.
Terminal Post: This term refers to the post which the wire will
be wrapped around by the operator.
3W: This term refers to the three prong plug which is found at the
end of the 20 foot power cord.
2W: This term refers to the two prong plug which is found at
the end of the 20 foot power cord.
Unique Indexing Mechanism: This term refers to mechanism within
the wire wrapping gun which causes the wire wrapping bit to line up
in the same position every single time you wire wrap.
Unwrapping Direction: This term refers to direction you could
unwrap a wire wrap. This can be in a right hand direction or left direction
depending on the direction the original wrap was done.
Voltage: This term refers to an electric potential or potential
difference expressed in volts. Any country may be using 110, 115, 120,
220, 230, 240 or even 48 volts for the electrical power source.
Wall I.D.: This term refers to the inside diameter of a wire
wrapping sleeve.
Wire Diameter: Same as wire size; refers to the actual diameter
of wire with insulation.
Wire Gauge: This term refers to the size of the wire as indicated
by the terms AWG (American), SWG (British) or mm (metric version). Wire
gauge of 18 AWG would convert to .0403" (1.022mm) of bare wire.
Wire Size: Same as wire diameter; refers to the actual diameter
of the wire with insulation.
Wire Wrap Bit: This term refers to a wire wrap bit which consist
of a terminal hole and a wire trough in which the wire to be wrapped
is placed. When this wire wrap bit is used in conjunction with the proper
wire wrapping sleeve the operator will obtain a perfect wire wrap to
the terminal post.
Wire Wrap Sleeve: This term refers to wire wrap sleeve which
consists of a straight tube which may or may not be tapered at the end.
When this wire wrap sleeve is used in conjunction with the proper wire
wrapping bit the operator will obtain a perfect wire wrap to the terminal
post.
Wrap(s): This term refers to how many times an insulated or bare
wire is wrapped 360 degrees around a terminal post. A 1/2 wrap would
mean that the wire went around the terminal post 180 degrees.
The
wire wrap information and graphics were provided courtesy of Standard
Pneumatic at www.stdpneumatic.com
and OK Industries, Inc. at www.okindustries.com.
Return
to Top of Page
|
|